Delve into the world of isolators in pharmaceutical manufacturing! This guide explores how these sealed enclosures elevate aseptic processing. We unveil isolator applications for containment & aseptic operations, along with key features like positive pressurization and bio-decontamination.
Explore considerations for integrating isolators into complex filling lines and sterility testing. Empower your decisions for efficient and high-quality aseptic pharmaceutical manufacturing
Defining Isolators:
- An isolator is a sealed enclosure with integrated physical barriers, designed to maintain leak-tight integrity through pressure testing.
- It creates a near-complete separation between the product, production equipment, personnel, and the surrounding environment.
- This allows for aseptic manipulations to be conducted within the isolator without compromising sterility.
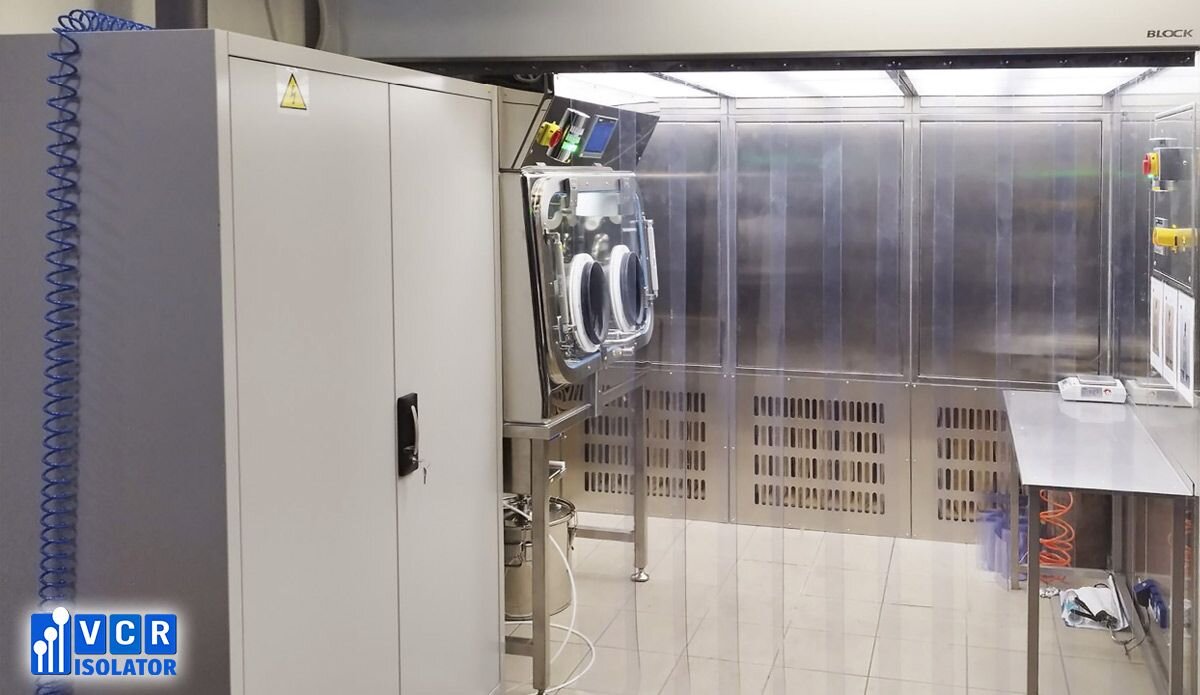
See more: Compounding Aseptic Isolators
Isolator Applications in Pharmaceuticals:
The term "isolator" encompasses a diverse range of equipment with distinct purposes:
- Containment Isolators: These isolators prioritize the safe handling of hazardous materials, aseptic or non-aseptic. They typically employ negative pressure to contain these materials.
- Aseptic Isolators: These isolators are designed to provide a controlled, microbiologically-clean environment for aseptic processing activities. They utilize positive pressure and may incorporate decontamination procedures using gas-based methods.
Key Features of Aseptic Isolators:
- Positive Pressurization: Aseptic isolators maintain a positive internal pressure environment with HEPA-filtered air ensuring unidirectional ISO 5 airflow within the workspace.
- Air Recirculation and Cleaning: Most aseptic isolators feature air recirculation systems with automated or manual cleaning protocols.
- Bio-decontamination: Automated cycles, often utilizing vaporized hydrogen peroxide, are employed for bio-decontamination within the isolator.
- Access and Integration: Access to the isolator is achieved through sterilized transfer systems and glove compartments. Aseptic isolators can be situated within an ISO 8 cleanroom environment or a more controlled setting.
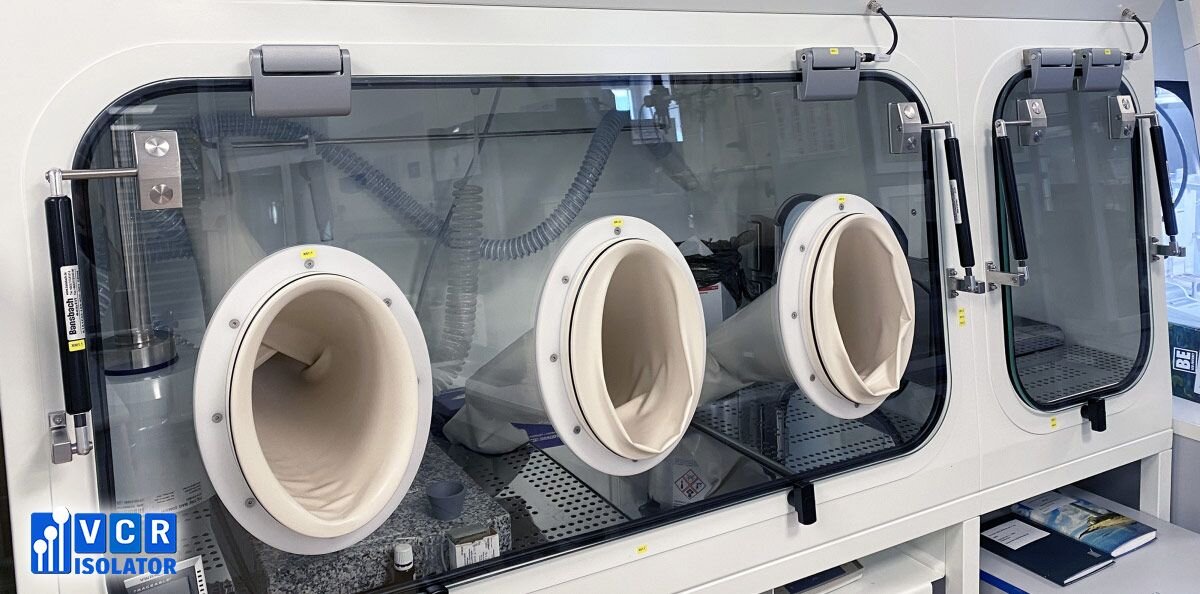
See more: Cleanroom Isolators Aseptic Processing
Benefits of Isolator Use in Pharmaceuticals:
- Enhanced Product Quality: Isolators minimize contamination risks, leading to higher product quality and sterility assurance.
- Reduced Operating Costs: Compared to traditional cleanroom setups, isolators can offer operational cost savings.
- Increased Production Capacity: Isolators can potentially enable longer production runs due to their enhanced containment capabilities.
Considerations for Aseptic Isolator Integration:
- Advanced Filling Lines: When integrating isolators into complex filling lines, careful management of interfaces between the isolator, filling machinery, and other equipment is crucial. This ensures smooth operation and simplifies control systems.
- Containment Isolators for Potent Compounds: For handling potent ingredients, isolators can be custom-designed with features like polished stainless steel chambers, inflatable seals, and other containment-specific elements.
- Sterility Testing Isolators: These isolators, typically equipped with two to four glove ports, are specifically designed for sterility testing of pharmaceutical products.
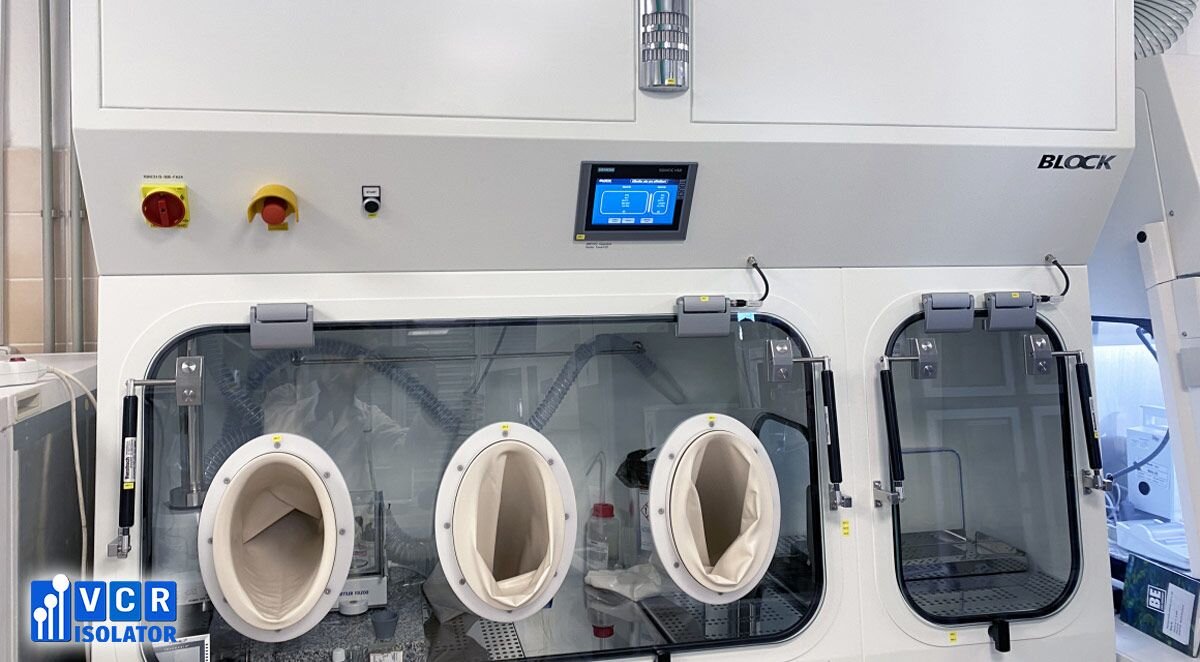
See more: Key Considerations When Selecting a Pharmaceutical Isolator
Conclusion:
Isolators offer significant advantages in aseptic pharmaceutical manufacturing. Understanding their functionalities and diverse applications empowers pharmaceutical professionals to make informed decisions regarding their integration into aseptic processing workflows.