This guide explores isolators, specialized clean air devices used in cleanrooms to further shield products from contamination.
Unveiling isolator configurations, diverse applications in aseptic processing, and key considerations for their use, this article empowers professionals in pharmaceutical and medical device manufacturing to make informed decisions about integrating isolators into their workflows.
Beyond Unidirectional Airflow: The Need for Isolators
While unidirectional airflow protects processes from airborne contaminants in cleanrooms, some applications require additional safeguards. Isolators function as physical barriers, further shielding products, personnel, and equipment from external contaminants. They offer several advantages over traditional cleanroom setups:
- Enhanced Sterility Assurance: Isolators boast built-in air filtration systems, reducing particle counts within the enclosed workspace. Their compact size facilitates decontamination using gas or vapor sterilization methods.
- Alternative to Sophisticated Cleanrooms: Isolators can serve as substitutes for complex cleanroom infrastructure in certain scenarios. This translates to cost savings on construction and maintenance.
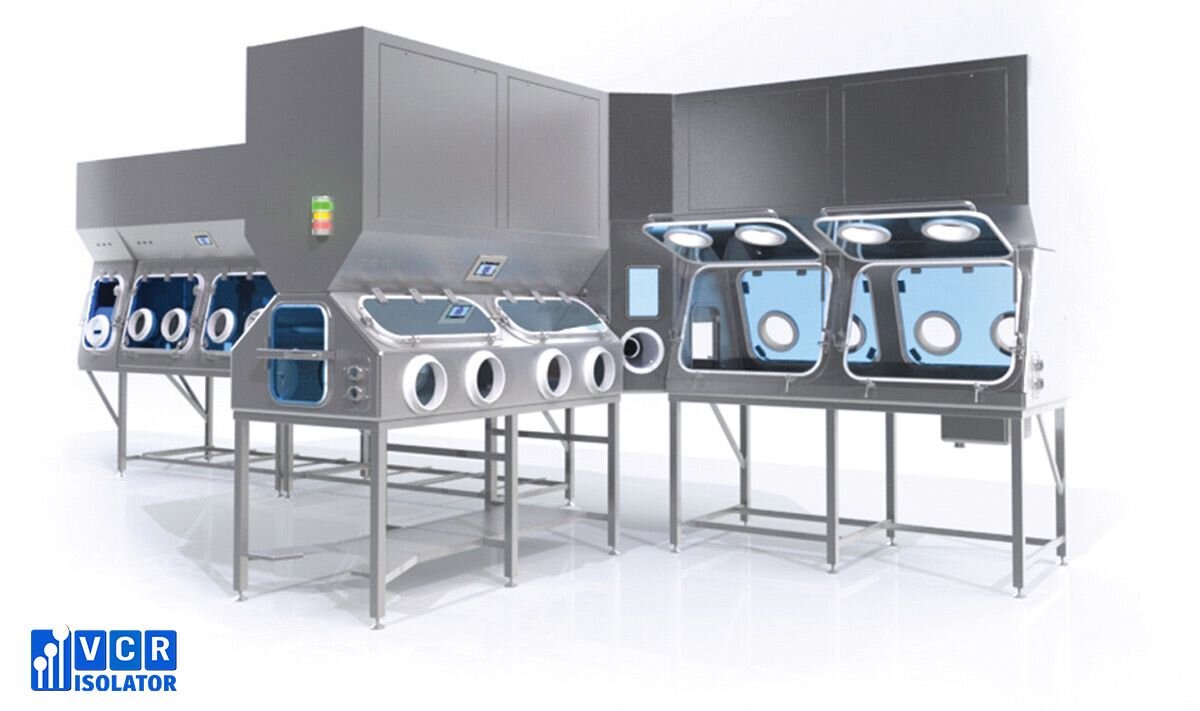
See more: Compounding Aseptic Isolators
Isolator Configurations: Closed vs. Open Designs
- Closed Isolators: Fully sealed enclosures offering the highest level of protection. However, their operation can be time-consuming due to restrictions on material entry and exit.
- Open Isolators: More prevalent for aseptic procedures involving frequent product transfers. Specialized ports maintain a positive air pressure gradient, preventing contamination ingress.
Filling, Transfers, and Beyond: Diverse Applications
Isolators find application in various aseptic processing tasks:
- Filling Operations: Sterilized products or containers are transferred using rapid transfer ports or airlocks, sometimes incorporating sterilization features.
- Transfer Isolators: Mobile enclosures for transporting sterilized materials without compromising sterility.
- Aseptic Assembly: Isolators can be used for assembling sterile medical devices.
- Sterilized Environment Testing: These units can maintain a controlled environment for sterility testing.
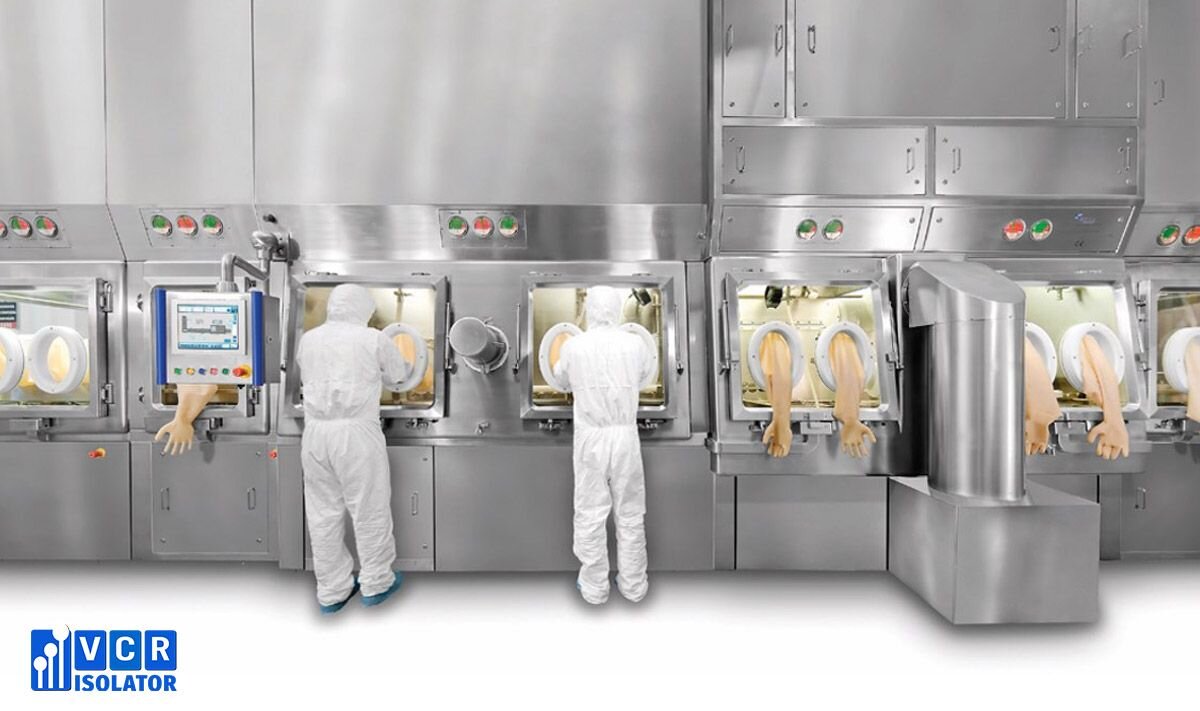
See more: Considerations When Selecting a Pharmaceutical Isolator
Manual Operations: Balancing Efficiency and Containment
Isolator processes often necessitate manual intervention. Workers can access the workspace through:
- Half-Suits: Airtight protective garments attached to the isolator, allowing personnel entry from below.
- Glove Ports: Sleeves enabling technicians to manipulate products or instruments within the isolator.
While glove ports are common even in automated setups for maintenance or adjustments, minimizing manual interventions is crucial. Glove failures pose the biggest contamination risk for sterilized materials.
Advantages and Considerations for Isolator Use
Isolators offer distinct benefits:
- Alternative to ISO Class 5 Cleanrooms: They can function effectively within a Class 6 or 7 cleanroom, eliminating the need for a more expensive Class 5 facility.
- Enhanced Decontamination and Monitoring: Isolators are generally easier to decontaminate and monitor, promoting sterility assurance.
However, some limitations exist:
- Flexibility: Isolator design requires careful planning due to their fixed physical configuration.
- Maintenance Considerations: Enclosed machinery within the isolator necessitates high reliability to minimize maintenance disruptions. Glove port and half-suit access should be designed for ease of use during production runs.
- Worker Comfort: For continuous manual operations, isolators need to be configured with worker comfort in mind.
In conclusion, isolators are valuable tools for enhancing aseptic processing within cleanroom environments. Understanding their functionalities, configurations, and limitations allows for informed decisions regarding their integration into aseptic manufacturing workflows.
See more: Isolator Aseptic Processing in the Pharmaceutical Industry